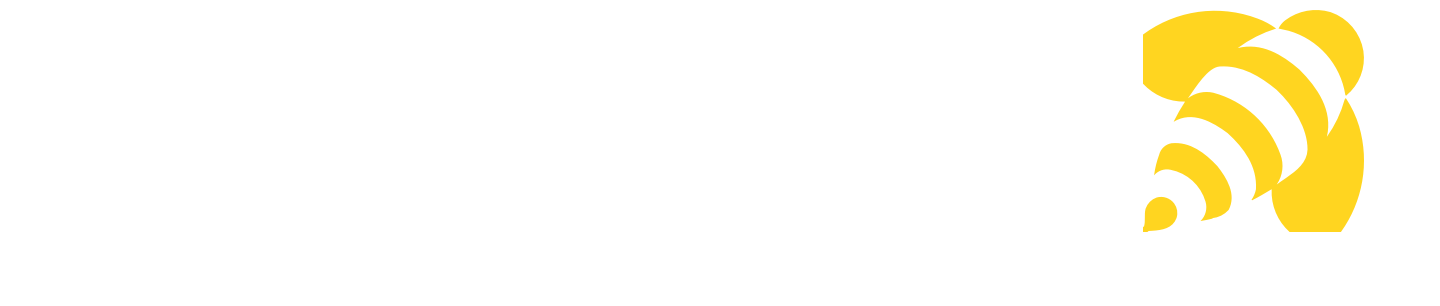
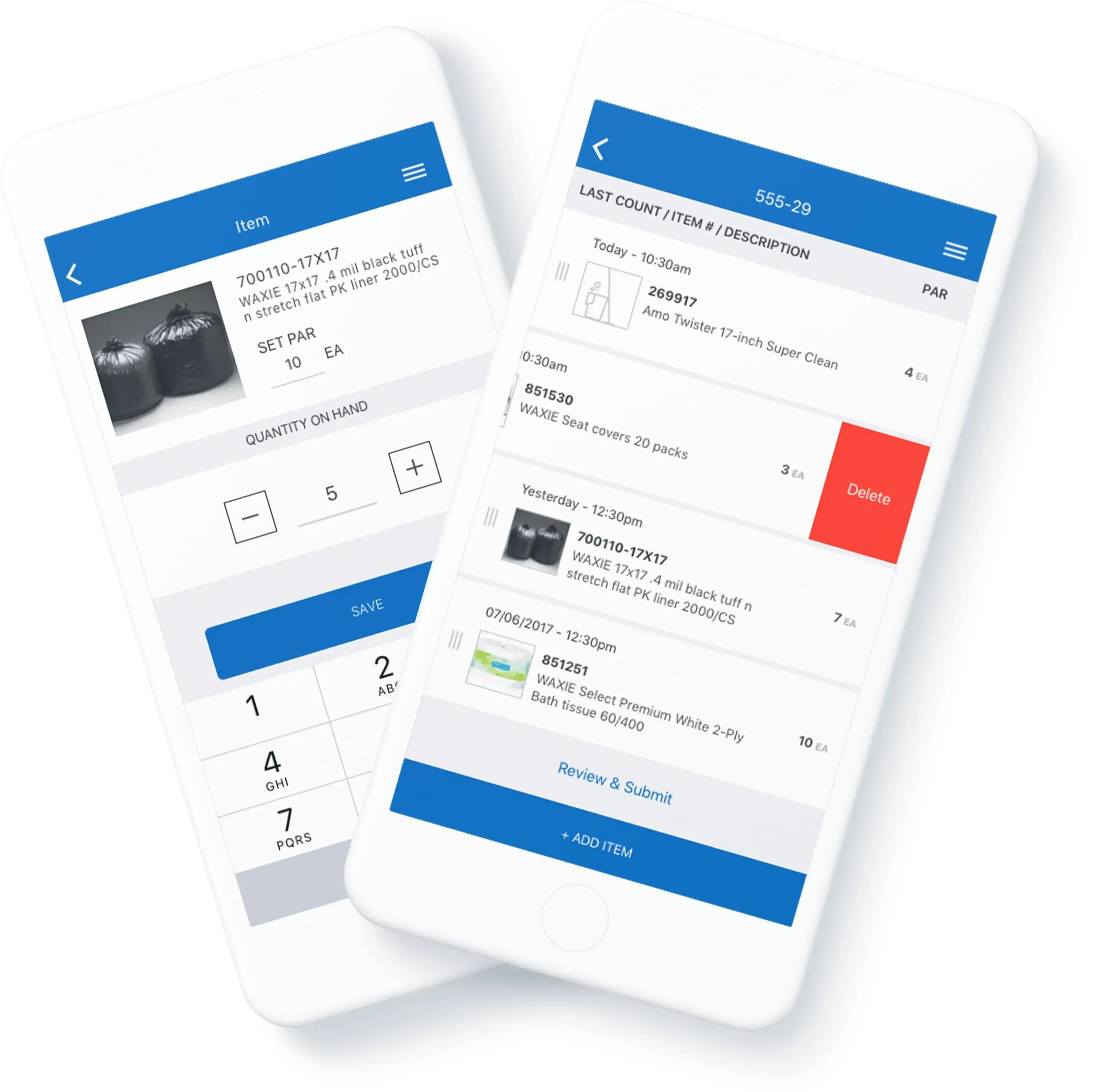
The Challenge
WAXIE’s existing app consisted of outdated 32-bit technology that resulted in order errors and would no longer be supported by new iOS and Android updates. The technical architecture had to be revisited and WAXIE was also seeking to introduce new functionality that would enable users to place orders and update clients' inventories in real time.
WAXIE didn't have the internal resources to complete the design and architecture of the project, so they sought out a digital transformation partner. Due to previous challenges encountered with an offshore firm while building version one of the app, they were specifically looking for a local company to take ownership of the project.
THE SOLUTION
Inventory Management
WAXIE partnered with Seamgen to complete a design and technology overhaul of their mobile app and web portal. With the use of Xamarin.Forms, a cross platform UI toolkit, Seamgen was able to leverage a single codebase that worked across iOS and Android devices. Beyond an improved user experience, Seamgen successfully integrated the application with WAXIE’s established back-end system. To resolve for the issue associated with order input errors, Seamgen developed a checks and balances system which eliminated the possibility of such mistakes.
Through efficient resource allocation and a strategic technology solution, WAXIE achieved significant cost savings. WAXIE’s final mobile app was valued 65% higher than the actual cost. Seamgen designed and developed an updated mobile app that WAXIE’s customers love using.
“My first impression of Seamgen was these guys are experts. The team was both impressive and fun to work with.” - Aaron Gerraughty, Vice President of Information Technology
Automated Processes
Seamgen built the application’s back-end to facilitate the inventory and reordering process. The WAXIE inventory managers are now simply responsible for reporting the quantity of product(s) remaining and the app will determine if an order needs to be created. By eliminating steps throughout the process, Seamgen was able to streamline operations and reduce overhead costs.
As a company that continually seeks to improve the quality of their products, it was important for WAXIE to have the ability to add or remove products from their catalog. Seamgen integrated the product catalog and it is updated daily to ensure that distributors and inventory managers have access to the latest equipment.
Streamlined Operations
In order to maximize efficiency, Seamgen implemented a barcode scanner so that inventory managers wouldn’t have to search for product names. They now have the ability to quickly scan a barcode to identify the exact product and submit their inventory check.
Offline Functionality
Since it’s not uncommon for the inventory managers to be behind metal doors or out of reach from a cell network, the application required offline functionality. Seamgen developed the application to enable users to count and track inventory offline, seamlessly submitting the order once the user was back in cellular range.
Tech Stack
- Xamarin.Forms
- C#
- Web API
Technical Approach
In order to ensure that features and functionality would remain the same and lessen the impact on current users, the Web API could not be heavily modified. Additions to the Web API introduced the ability to edit the product catalog in real time and improve order management. Since the application did not require compelling visuals or animations, Xamarin.Forms was leveraged to remain budget friendly, maintain a purposeful build, and provide an optimal experience for users across all platforms. The same tech stack was used across all platforms, using C# on both the frontend and backend of the program. This strategy allows for the mobile source code to be easily adapted, enabling WAXIE to make necessary modifications as their requirements evolve.
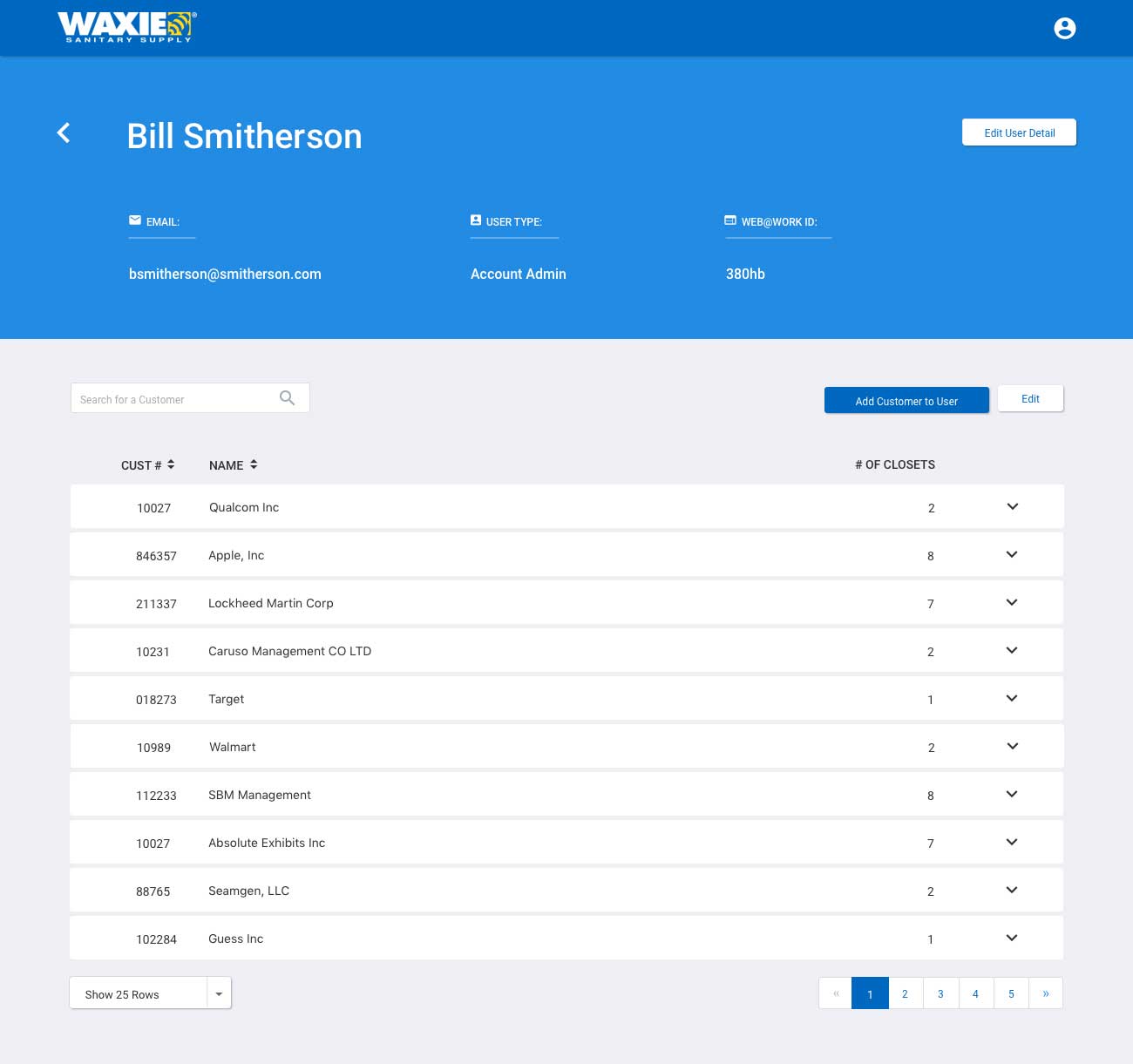
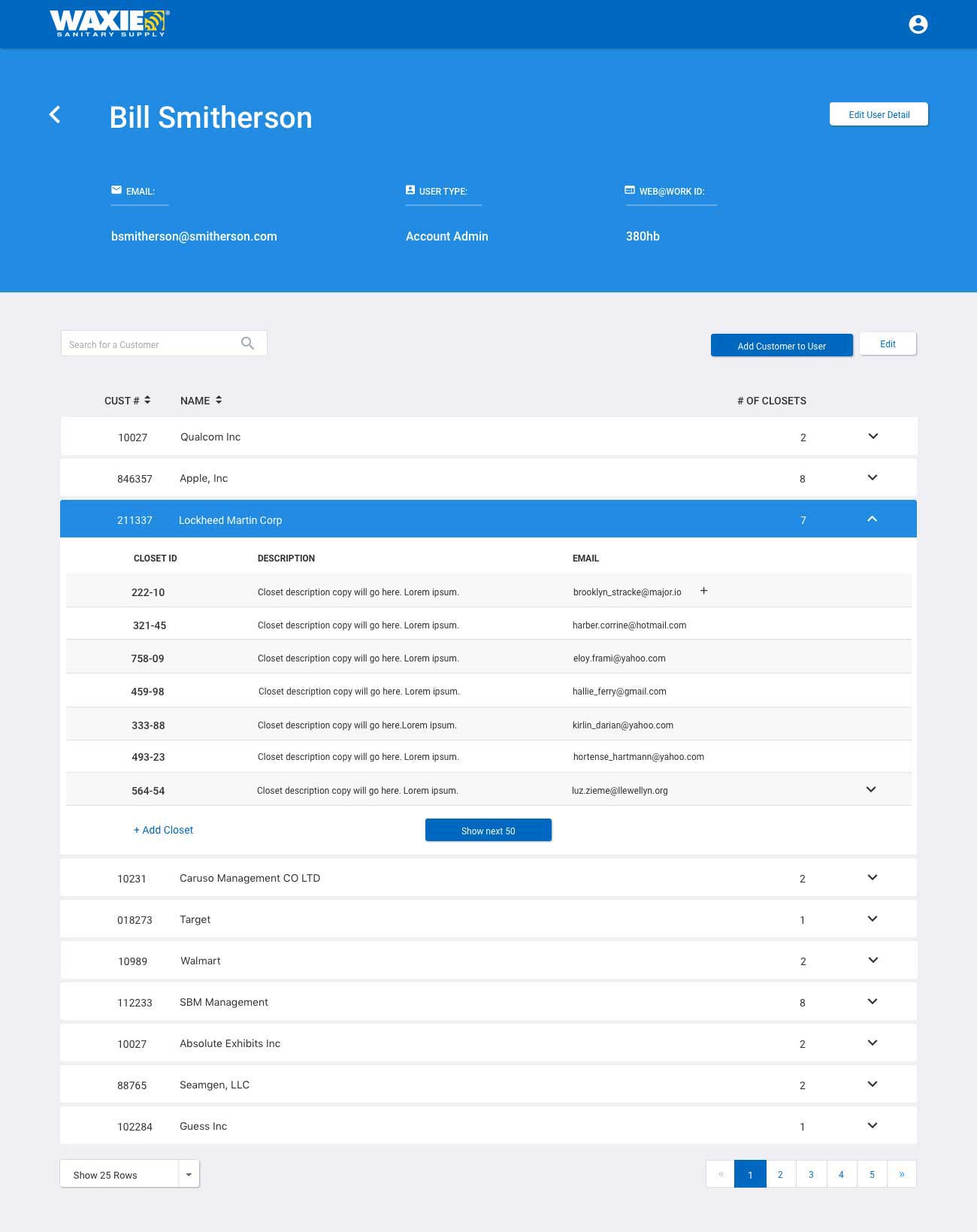